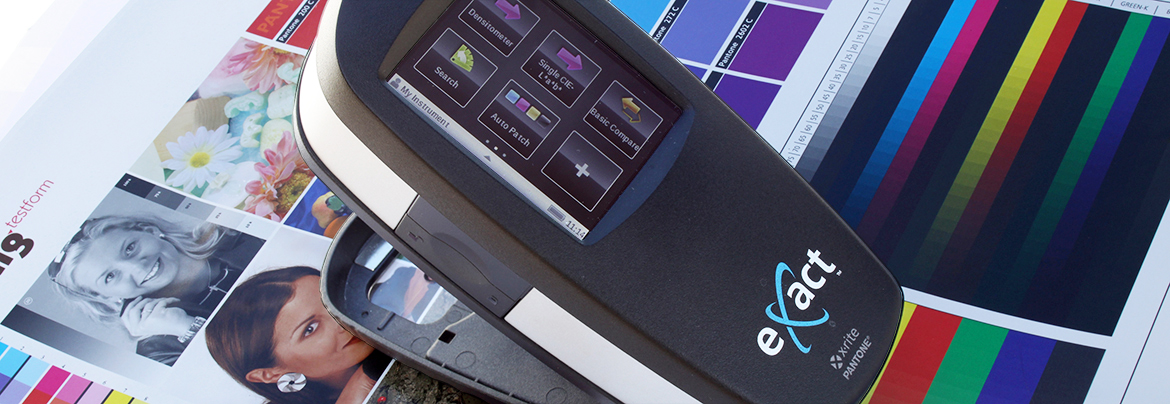
Lean Manufacturing from Berkshire Labels – Colour Management
News Article 2 of 3
To understand how Berkshire’s press operators are able to perform job changeovers in just 10 minutes, you have to look beyond the highly automated P7 as this is only one (but a significant) part of the story.
The entire process has had a complete overhaul to enable fully automatic production that sees a Shuttleworth MIS seamlessly integrated with the Esko workflow and GMG Color profiling and proofing solution. The key element here is a colour management system that enables Berkshire to send out certified contract proofs that have been produced to the FOGRA 39L standard for coated materials (and 47L for uncoated materials).
Colours can be reproduced to a Delta E of less than 2, no matter how the job is printed, and irrespective of whether the colour is known or not. X-rite spectrophotometers and IQC software can scan and match any colour sample which can then be made up in the pre-press department. All presses have been fingerprinted and profiled to the set standard, so print quality is not a deciding factor when it comes to choosing the type of press for a given job.
Fewer and fewer clients come to print pass at the Hungerford operation these days. Having such stringent parameters in place means that there is no need for signing off on press. With guaranteed certified contract proofs, what you see is what you get, and spectral data from the actual print run can be reported back to confirm that the colours are on target. ‘We have spent a lot of time and money to perfect our closed loop colour management system and we aim for a Delta E of 1.5 or less,’ said Mr Roscoe, ‘so there is simply no reason to approve a job on press and we certainly won’t start changing it once it is running.’ He continued to say that ultimately he is aiming to have a fully ISO certified colour management system accredited this year.
Having taken digital print to its highest level over the last five years, Berkshire Labels is now in the midst of a substantial investment programme on the well-established flexo side of the business. Closed loop colour control, working to exact standards and a top of the range new press are the tools that will take the company into next generation flexo printing.
Copyright Neel Madsen FlexoTech Magazine March 2016
See article 3 of 3 Lean Manufacturing from Berkshire Labels – Digital and Flexo in Harmony